The process of reusing materials is both economically and ecologically sound. Currently, 3 out of 4 PET bottles in Austria are already collected correctly and returned into the recycling loop. A large proportion of these are processed by PET to PET into food-grade recyclate. This allows the valuable resource of PET to be reused as the base material for the production of new PET bottles.
Recycling in Müllendorf
After used PET bottles are disposed in the designated containers, they are sorted by colour and pressed into large bales and make their way to Müllendorf via the relevant collection system. A bale weighs around 250 kg and contains approximately 10,000 PET bottles.
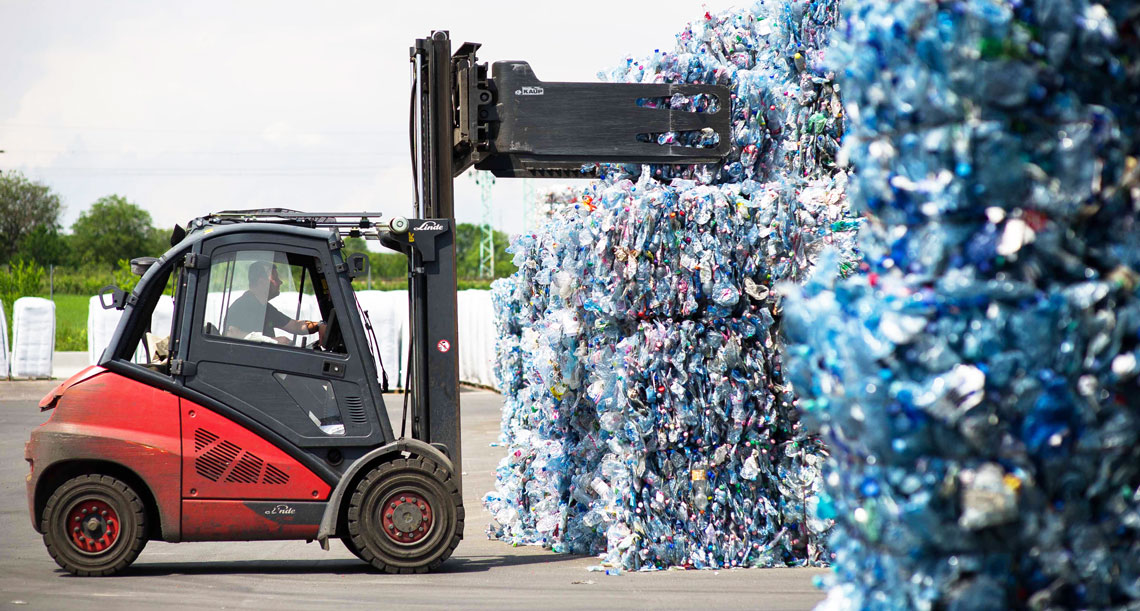
The incoming bottles go through automatic quality sorting and are inspected by our staff. Non-beverage bottles and foreign materials are sorted out manually. The bottles are only shredded in the mill once it is certain that only PET (beverage) bottles are contained in the process. From this point on, the tiny fragments are referred to as PET flakes. They now go through both a dry and a wet cleaning process. Contaminants and dirt are removed via intensive washing. The bottle particulates – a mixture of bottle cap fragments and PET flakes – can then be separated from one another based on their specific weight difference and dried.
The flakes are once again thoroughly cleaned while preventing damage to the material in the patented URRC process (United Resource Recovery Corporation). Because the flakes must comply with the highest food industry standards, it is crucial to remove any flavouring agents. In order to guarantee this, the uppermost layer of the flakes is removed in a unique process. After this, the material goes through deep cleaning a special rotary kiln. Once they have been rinsed with clear water, the flakes are dried and sorted again. Any PET fragments that may have become discoloured during treatment are sorted out.
In a second treatment process, the Starling process, the washed PET flakes are heated up to the point that they become liquefied. The liquefied PET mass – called molten mass – is pressed through a fine screen changer and then shaped into small pellets. In order to achieve the required food-grade quality here as well, a deep-cleaning step is also performed in the SSP (solid state process) reactor at this stage. Now this recycled material also meets the highest quality standards of the food industry.
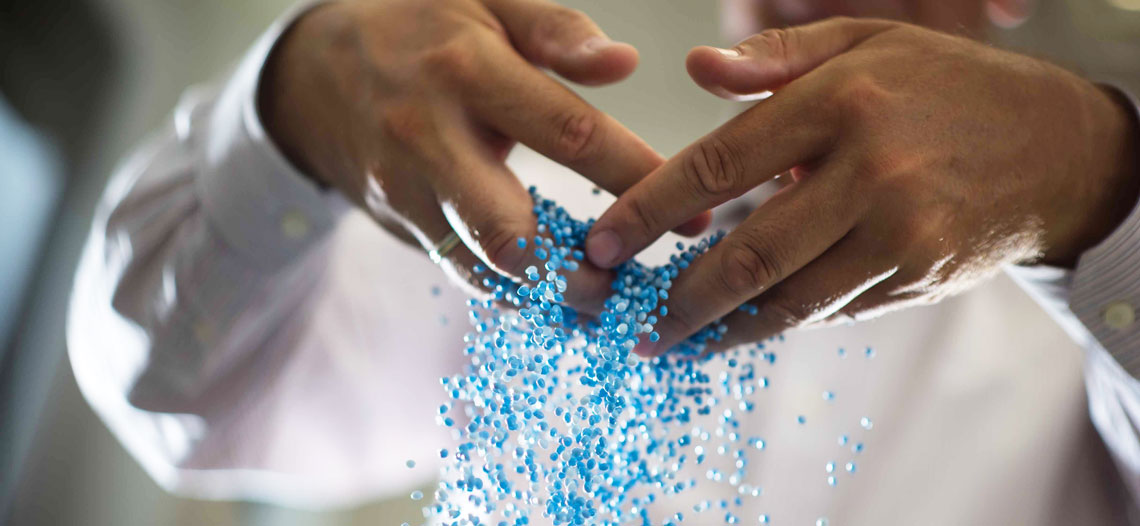
The extracted recycled material has nearly the same characteristics as new material. The PET flakes and PET pellets are filled into so-called big bags or in loose form in the silo and are used instead of new PET in the production of new PET bottles by preform and bottle manufacturers. The entire process – from the inbound delivery of the bales (collected PET bottles) to the outbound delivery of recycled PET in big bags – takes only eight to ten hours. Today, PET bottles are made of around 30-40% recycled material, and the percentage can also be significantly higher depending on the size and shape of the bottle.
All about flakes and pellets
The joint processing of both types of recycled material (flakes and pellets) combines the advantages of maximum purity and colour quality with optimal processing conditions.
After the first washing stage, PET flakes are cleaned in accordance with the highest food industry standards in the patented URRC process (United Resource Recovery Corporation), which is energy-efficient and prevents the material from being damaged. Even after the intensive cleaning, the basic shape of the flakes is retained and the material reaches optimal recycling quality thanks to the heat-efficient cleaning.
PET pellets are PET flakes that have been further processed. In the so-called Starling process, the washed flakes are first dried, then melted, filtered through a fine screen changer, pressed through a nozzle plate, cut into pellets, and finally cooled under water. Then the pellets are crystallised and deep-cleaned in the SSP step (solid state process).
Cutting edge technology for the good of the environment
For us, it is important to use the most modern environmental technology in the recycling process at our PET to PET plant. One good example is our careful approach to water consumption, which is reduced to a minimum through a nearly fully closed-loop water cycle.
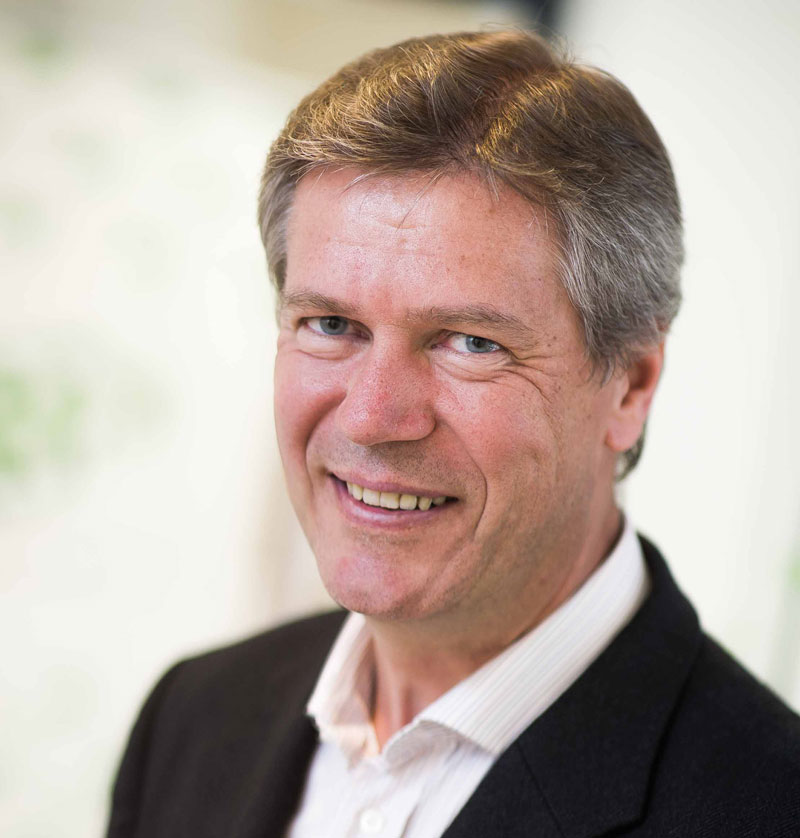
“Ever since our company was founded in 2007, we have been ensuring the conservation of resources and efficient recycling through state-of-the-art technology – and we are living up to this standard now more than ever before. Our company is setting the standard in Europe in terms of the processing and the sales volume of PET bottles. At the same time, however, the ever-increasing collection discipline of the Austrian public contributes to our successful and productive PET recycling system, thus extending the useful life of PET as a resource,” stresses Christian Strasser, Managing Director of the PET to PET recycling plant.
The Müllendorf recycling plant operates 24 hours a day in four shifts. Production is only halted one day a month in order to perform cleaning and maintenance work.